Wood chip traffic on the ACR primarily derived from the sawmills and Dubreuilville and Mead. Both mills were large sources of chip traffic – although not at the same time.
Newaygo Forest Products (Mead, ON)
In 1974 Newaygo Forest Products built a new modern mill 20 miles south of Hearst on the ACR at Mead to produce lumber and wood chips for export to the United States. The woodchips would be shipped to a paper mill in Appleton, Wisconsin.
To supply cars for this traffic the Algoma Central purchased 89 cars from National Steel Car in 1974, with unique ACIS reporting marks designating them under some customs rules or regulations for International Service. A further 23 cars with regular AC reporting marks were added in 1980.
These large capacity cars, the biggest cars on the ACR roster and painted a unique pale green colour with yellow end doors and “billboard” lettering cut a striking appearance, and travelling over almost the entire length of the railway and into Michigan and Wisconsin, there are several good photos of both of these car series available.
They seemed to ship up to about half a dozen cars at a time from Mead, and extra empty cars would often be stored in the siding at Horsey or Coppel, on either side of Mead.
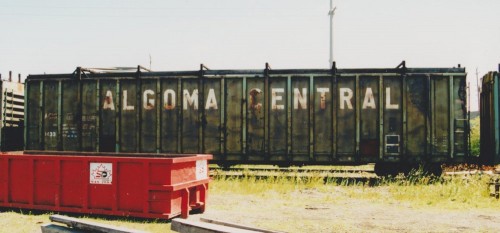
ACIS 1433, one of a few survivors from the Algoma Central’s woodchip car fleet at Steelton yard in 2001. Blair Smith photo.
The mill at Mead shut down in 1985 bringing this traffic to an end.
Dubreuil Forest Products (Dubreuilville, ON)
In about 1986 or 1987, Dubreuil Forest Products installed a new chip spur and loader at their mill at Dubreuilville to load woodchips for the pulp mill on the Canadian Pacific at Marathon.
Cars for this service were 52′-60′ gondolas provided from Canadian Pacific. Over 100 cars were provided, with empties stored in the sidings at Goudreau and Wanda north and south of Dubreuilville to protect the loadings at the mill.
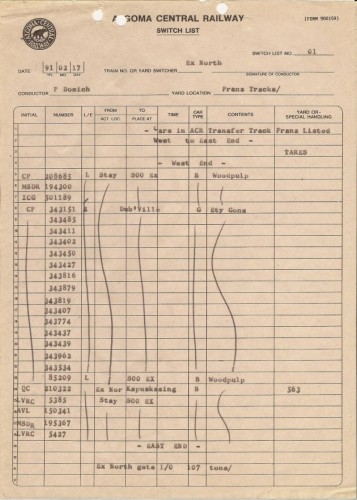
1991 switchlist showing cars in the transfer track at Franz. The dozen empty CP 343xxx series gondolas listed are woodchip cars for Dubreuilville.
Despite the large numbers of car loads involved, since they operated only between the interchange at Franz and the mill at Dubreuilville about 10 miles south, and both locations being a bit more than just slightly off the beaten path, this traffic wasn’t too visible and I haven’t seen much in the way of photographs of these cars in ACR trains, unlike the much more visible AC/ACIS woodchip gondolas that were used to service the Newaygo mill. Fortunately the cars have been well photographed in other locations, particularly as many survivors have recently been used in tie service.
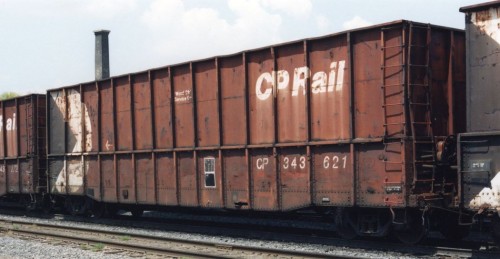
A common variation of CP’s woodchip gondolas rebuilt from a 52′ gondola with extended sides. Bill Grandin photo.
During the 1990s, the AC (and later WC) ran an weekday evening “Franz Turn” out of Hawk Junction to switch lumber and chip loads at Dubreuilville and the interchange at Franz.
The mill at Dubreuilville closed in 2007.
Lecours Lumber (Calstock, ON)
After Newaygo shut down their operations at Mead, the fleet of AC and ACIS woodchip cars were sold off, with many cars being transferred to Newaygo for use on other operations.
One place where ex-Algoma Central cars with Newaygo (NFPX) markings seemed to show up regularly in the 1990s and early 2000s was at the Lecours Lumber stud mill west of Hearst, on trackage now operated by Ontario Northland. These chips apparently headed down into the US somewhere, so by a curious twist of fate, these ex-Algoma Central cars continued to operate over the former Algoma Central rails for several years.
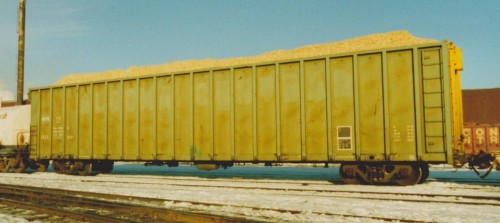
NFPX 1511 with a load of woodchips at Steelton yard, 1999. Blair Smith photo.
I’m not sure when this service ended (or if indeed it still continues on a periodic basis) but in my few visits to the area over the last few years I’ve never seen any chip cars.