When the Algoma Central dieselized in 1951-52, their varied roster of steam locomotives was replaced by a pair of SW8 switchers for duties in Steelton yard, and a fleet of 21 all-purpose GP7 road switchers for mainline power.
Unlike many other larger railroads that acquired some engines with optional built-in boilers to provide steam heat for passenger trains, the ACR opted for a standardized fleet of dual-purpose locomotives and none of their locomotive were ordered with steam generators. Instead, the ACR converted several cars in the Steelton car shops to act as stand-alone steam generators for passenger trains, allowing the entire locomotive fleet to be used in either freight or passenger service. Four cars, numbered AC 71-74 were custom built in the car shop on the underframes of old 40′ steel-braced wooden boxcars. One additional car, AC 76, was converted from baggage car 204, itself a conversion from a former US Army troop sleeper car from the Second World War.
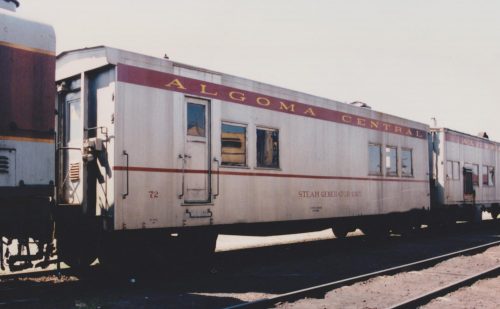
AC 72 at Steelton Yard in the early 1990s, courtesy Blair Smith. Coupled to the left and right are other steam generator cars converted from an old Northern Pacific steam locomotive auxiliary tender and a former US Army troop sleeper car.
I haven’t been doing much modelling work this summer on account of on top of the normal summer busyness I moved into a new home in mid-August. So there’s been a lot of preparation and settling in over the last while. Over the Labour Day long weekend however I was able to get a couple of projects out, and one of them is this scratchbuild of a pair of the home-built generator cars. AC 71 and 73 were retired and scrapped in the mid-late 1970s but 72 and 74 lasted in service through the 1980s and into the mid 1990s. Since the ACR locomotives did not have generators, every ACR passenger train would run with a generator car so I definitely have a need for some of these unique cars.
I actually started the sides and ends for this pair of cars quite some time ago, but have never wrote about them before now. The sides for one of the cars are almost complete, and the sides for the second car are still just blank rectangles requiring windows to be cut out yet. I did however do the basic fabrication for all four ends for the two cars. On the holiday Monday I was able to do the basic assembly of the first car using the completed sides.
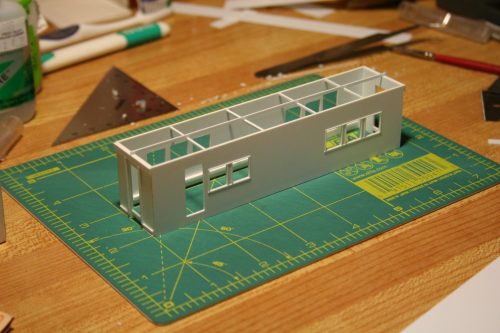
Sides and ends assembled, showing 2×6 ridge line for roof.
The dimensions for the sides and the window locations were worked out from photos and an ACR painting/lettering diagram in the Sault Ste. Marie Public Library Archives. It’s designed to fit over an Accurail underframe for their 40′ wood boxcar kit. (I’ve used this kit to model a trio of AC 3100-series boxcars, and these generator cars were built using underframes from retired cars from this series.)
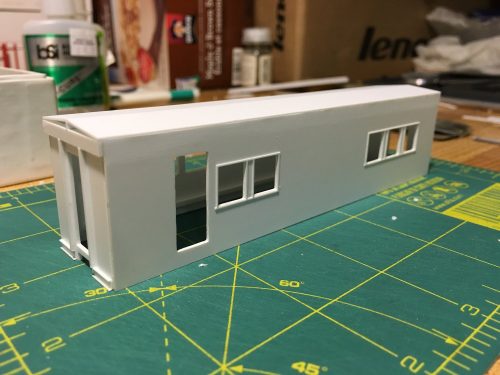
Basic car assembled with sides, ends and roof.
The sides and ends are cut from .040″ styrene, with basic end details added using various sizes of styrene strip. There’s a lot more to do there yet though, so stay tuned. The side windows have some framing trimmed around the openings using thin strip to replicate the prototype frame. More work needs to be done yet to actually model the window sashes within the frame, and to frame and model the doors.
Note that the car sides are not mirror imaged – the door is to the left-hand end on both sides.
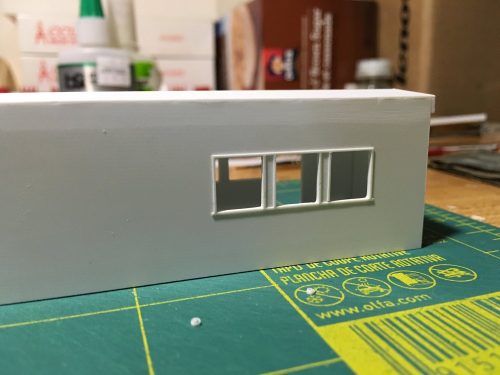
Detail of window framing.
That’s about as far as I’ve gotten so far, although I’m hoping to chip away at making more progress on this project over the next week or so. Probably starting with getting the sides for the second car completed so that both cars will be at the same point in order to progress forward with the finer detailing on both cars at once.