Catching up on some projects that I worked on a while ago, but haven’t posted to this blog recently. One of those projects is my pair of scratchbuilt ACR steam heater cars.
I assembled the bodies, and then these sat for a while while I worked out the roof details.
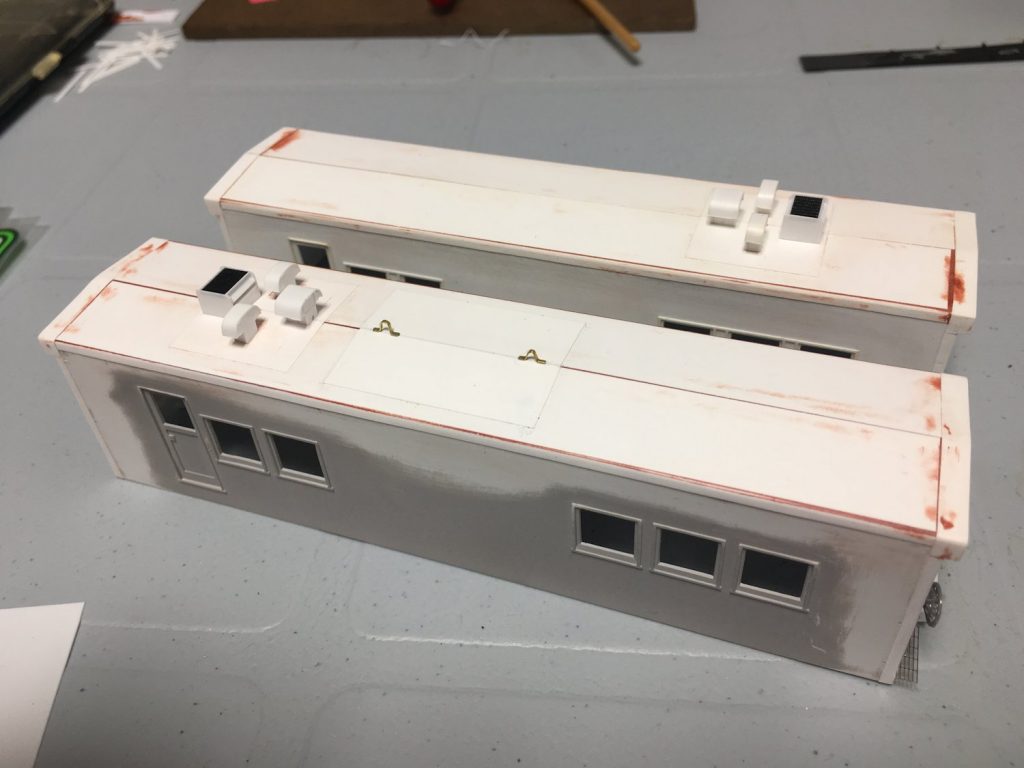
The main details are of course the various vents for the steam boiler. These are placed on top of a hatch on the roof. The hatches were made with .005″ styrene sheet glued to the surface of the roof. *Good* roof photos are hard to find, most of the detail is only worked out from side or oblique shots, but I have enough to go on to make out the size and positions of the hatches. Photos also seemed to indicate the one car had an extra hatch in the middle of the roof (not sure if and/or when this was added to the car, so it may or may not have been there in the mid-eighties, but it makes for a good visual variation). A couple of bits of flat brass wire formed into lifting loops finishes off the middle hatch.
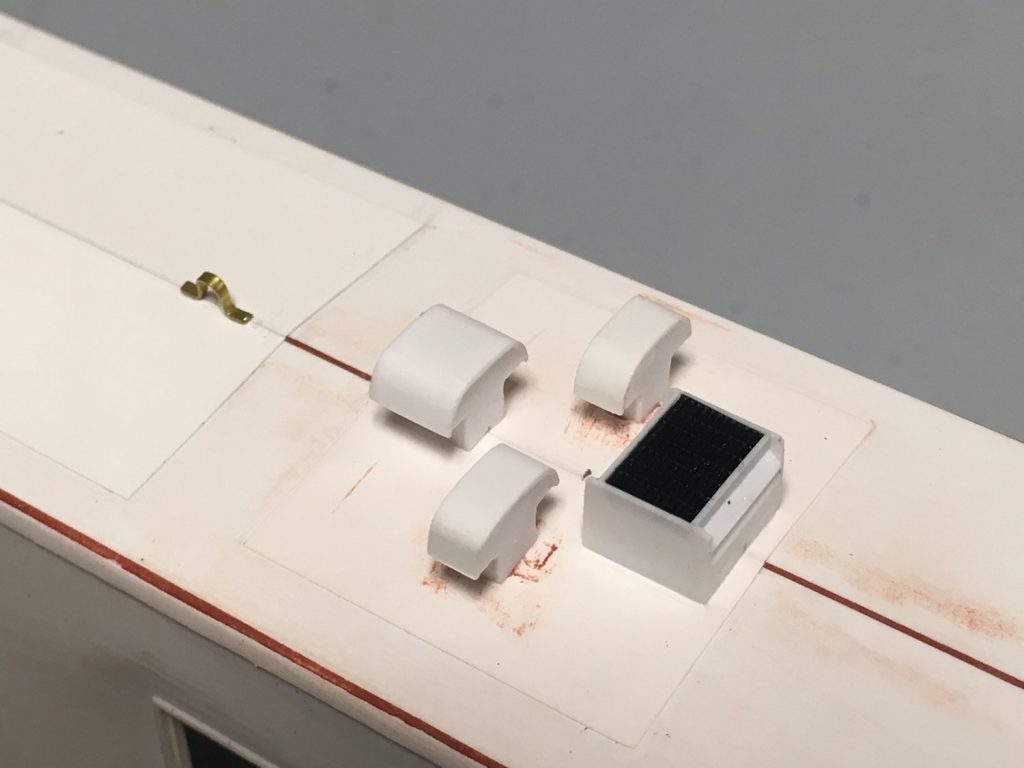
The actual steam vents were an interesting challenge to build from .010″ styrene sheet and strip. The mushroom-shaped stack ends were carefully cut and filed to shape, then assembled with simple sides, and then the top was added by curving strips cut from styrene sheet over the top. Liberal use of styrene cement and patience holding the part in place while the solvent evaporated and dried was involved.
The boxy vent was fairly simple by comparison, assembled from assorted .010″ strip and sheet. The “grillwork” on top was cut from a scrap piece of walkway material in my junk/parts box.
There’s not much more to do on this pair of cars any more before painting them, but I have a few other passenger car related projects in the works as well, and I’ll probably hold off on the painting for a bit yet until I can put a bunch of them into the shop. Need to get some appropriate shades for the grey and maroon paint…