This week I managed to take the next step forward on the ends for my (current) quartet of 40′ end-rack pulpwood flatcars, finishing up the major framing on the end of the rack.
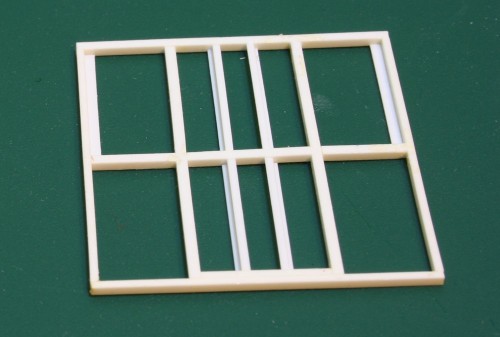
Note that the inner-most vertical members on the prototype are Z angle, not square tube or bar stock like the rest of the frame. Unfortunately I couldn’t find any commercially available Z strip in the .040″ thickness I needed to match the rest of the framing; Plastruct makes some down to 1/16″ but that’s still far too large by at least 50%.
What to do when you can’t get the angle stock you need? Well, simply fabricate your own out of plain strip. To make the fabricating process easier, cleaner and more precise, I built a jig using a couple sizes of styrene strip sandwiched between a bit of scrap styrene for a top & bottom plate, with a space in the middle to feed through a pair of .010x.030″ strips (top and bottom flange) and a .010x.020″ (middle web) strip through the jig.
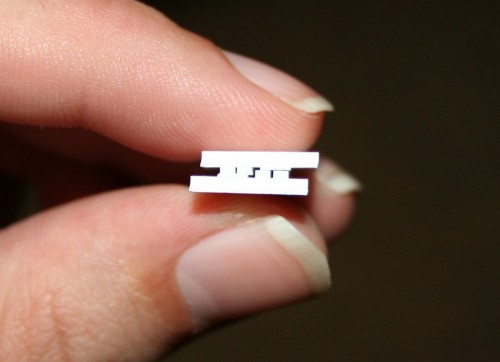
Once the cement on the jig set, I could fabricate the Z stock by inserting the strips into one end of the jig and slowly pushing them through out the other side, about a quarter to a half inch at a time and cementing them together with liquid cement applied with a very fine brush into the joint between the strips.
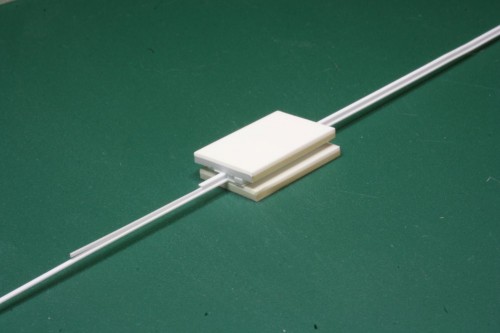
The result is a nice, solid structural shape that looks about as good as any solidly extruded commercial offering, and would have been extremely difficult or impossible to do free hand at such a small size.