In the 1980s, the Algoma Central rostered three types of 100-ton hopper cars in Wawa iron ore service: 100 of the distinctive and unique round-sided black hoppers in the 8000 series, built in 1971 by National Steel Car, 300 of the green rapid-discharge hoppers also built by NSC (using an Ortner Freight Car design under license) in 1974-75, and 30 “standard” triple hoppers acquired secondhand from the Ontario Northland Transportation Commission around 1978.
The Ontario Northland hoppers were part of a 72 car series ONT 6000-6071 built by NSC in 1971 and were used in iron ore service from Adams Mine at Dane, ON to a steel mill somewhere in Pennsylvania. For this service, triple hoppers were provided into a pool by Ontario Northland, Canadian National and New York Central (CASO and TH&B cars). Around 1977 or 1978 this particular service to Pennsylvania had either changed or ended completely, and the cars either went back into general usage by their owners (CASO cars were likely renumbered back to original NYC & PLE source series) or were sold off. 30 of the ONT cars were sold to Algoma Central in 1978; I’m not entirely sure where the other 42 ONT cars went initially, but today they can be found on the New Hampshire Northcoast Railroad in New England. When first acquired, the cars were just given AC reporting marks and kept their original numbers for a few years, but were later renumbered into the 8600-8629 series sometime around 1984.
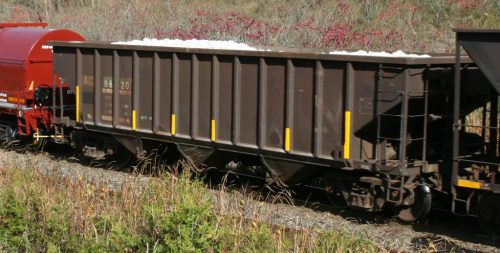
AC 8620 at Scotch Block (Halton Hills), ON October 18, 2008. Photo by David Graham. All the years of weathering have obscured the original colour and much of the lettering, but these cars were painted in the Ontario Northland’s dark green “Progressive” scheme.
While basically a standard design for a hopper, there’s no model out there that exactly matches this car. These are relatively modern welded cars built in the 1970s, but as they were intending to haul iron ore and rock, their size is much smaller than many other modern cars. Most models that are out there that are of an appropriate size tend to represent 90-ton cars a few decades older than these cars, with a different number of side posts/panels and riveted construction. One could accept a riveted car as a stand-in, but the difference in side panels causes issues for the spacing and placement of the lettering.
So, to solve this problem, I turn to my styrene supply to build a few of them for the fleet…
First of all, I spent time carefully working up my own scale drawings as a guide for this project. With the angles involved with the hopper bays, it’s a little more complicated of a build than a small shed or something. Using equipment registers I can find out the major overall dimensions, and using some relatively side-on photos available online, I was able to scale out a few dimensions and work up a drawing.
Actual dimensions of ONT 6000-6071 series, from ORER:
Inside | Length | 40’6″ |
Width | 9’8″ | |
Height | 6’0″ | |
Outside | Length* | 44’2″ |
Width** | 10’7″ | |
Height*** | 10’8″ | |
Capacity | lbs | 200,000 |
Cuft | 2700 |
* Over couplers
** At top of side
*** From rail head to top of side
The basic sides/end are constructed from .020″ styrene plastic sheet, with HO scale 4×4 side posts and an .060″ square top chord. To represent the angled bracing at the bottom, I cemented a strip of .060″ angle, open-side down along the bottom edge of the car side. (The bottom of the side posts are all cut off at a 45 degree angle with my Chopper.) General side dimension notes – top of side: 40’6″; top chord overhangs by 6″ for length of 41’6″; height of side: 7’6″, length of bottom of side: 31’6″ (length of bay cut-out: 4’6″), height of top ends, 2’9″.
Note the different spacing between the ribs at the middle of the car compared the outer bays – this was deliberate and I took a lot of time to try to make sure the panel widths were scaled out properly based on the prototype photos. I worked it out to about 25″ between the 4″ ribs (or 29″ rib centrelines) for the four middle panels and 30″ (34″ rib centrelines) panel width for the outer panels.
Since if I’m going to build one, I can build more than one; and if I build more than one, it’s efficient to build them all at the same time, assembly line style, so once I finish basic construction on all of the sides for the cars, I can move on to assembling the sides with the ends…
Note: for anyone working in N-scale, I found this model on Shapeways.
Why not use one for a mould and cast resin sides?
Well, I enjoy working in styrene, and in this case the sides are pretty clean with their welded lines and not incredibly difficult. Working in styrene will make it “easier” to glue the body sheets and fiddle bits together properly.